Which Block Do I Need?
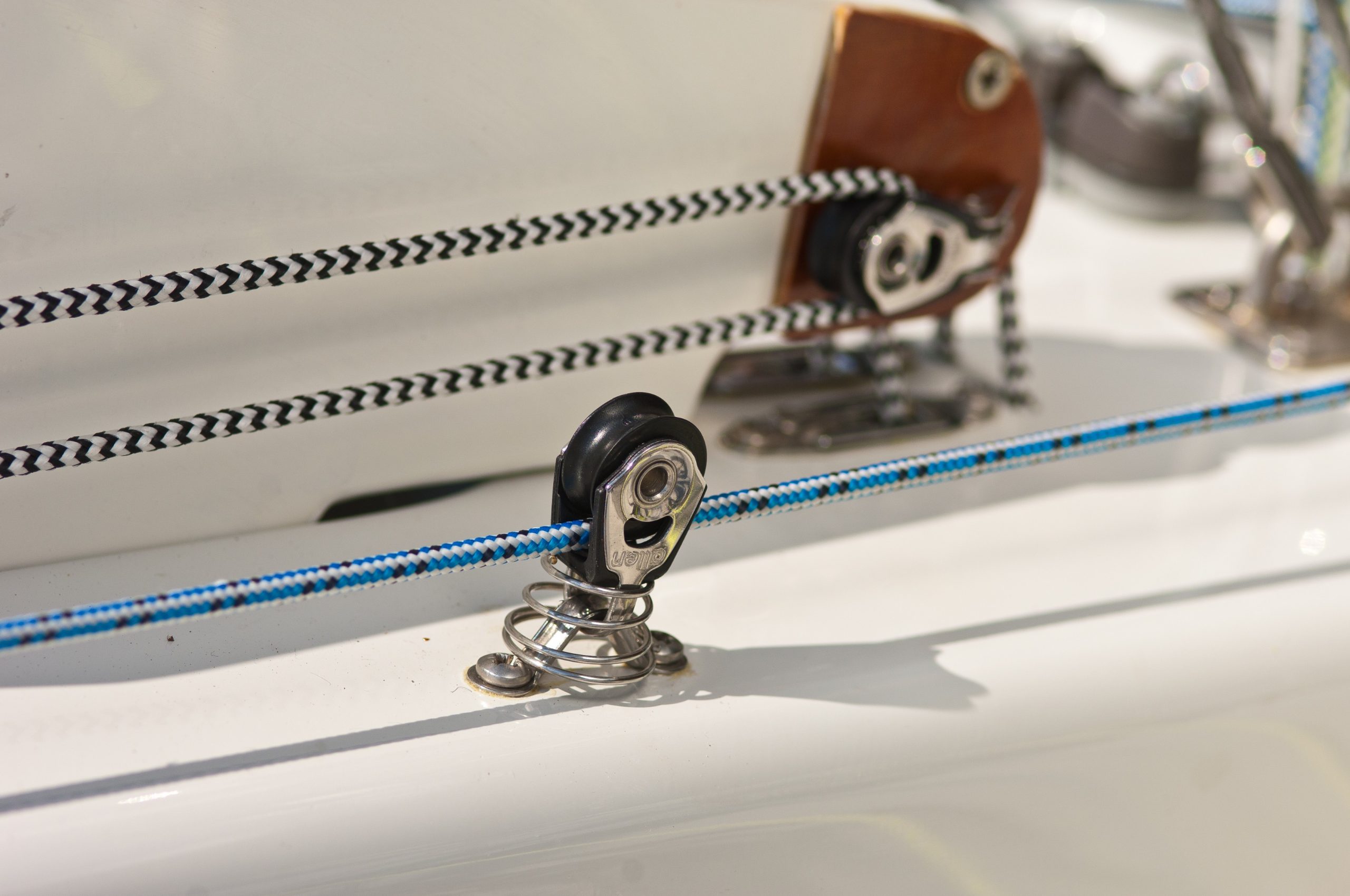
Choosing the correct piece of hardware when making a system upgrade or replacing a broken piece of kit can sometimes be more difficult than first thought. So, we have put together this article to try and help you make an informed decision on which block to choose.
Jump to
The most common reason for an aftermarket block replacement is usually down to breakages and, in most cases, sailors tend to stick to what they know and simply replace a broken piece of kit with a like for like swap. This method is usually the easiest option but, in most cases, isn’t the correct one.
Choosing a like for like replacement when the existing piece of hardware has already broken will usually lead to another major failure, in the same way, this means the piece of equipment your choosing isn’t designed for the job it performs. So, what factors should you consider when choosing a new replacement?
Firstly, determining which part of the block has had a major failure. Was it the strap, sheave or if it’s a block with an additional accessory such as a cleat mounting, swivel, hook or becket that has broken? Once you have determined which part of the block had the malfunction you should next look at how the block was being used and what might have caused it.
The most common reason for failure is because of overloading but you may also come across a block failure in a system where the rope has not entered the pully at the correct angle causing twisting or side loadings.
If you suspect the failure has occurred because of a twisting or sideloading issues, then you may need to consider replacing the broken part with something that will tolerate these issues better, for example, a swivel block. A swivel block will allow for better articulation and should rotate to accommodate for the bad lead angle. However, you may also need to rethink the system and perhaps add rope guides or lacing eyes to create a better lead for the rope into the block.
Overloading being the most common issue for a block failure is usually quite easy to resolve. With hardware becoming stronger and stronger with each new product that is being designed. If you’ve have had a failure in the strap of the block due to overloading, you should first check how the block was attached. Sailors love shackles, and why not! They’re easy to use and make attachment simple. However, when using a stainless-steel shackle with a block that has a stainless-steel strap you will notice that over time the strap of the block will start to tarnish where the two materials meet. This is where the metals are rubbing, causing heat from the friction and over time leading to a weakened state for the metal. Over a long period, this will lead to a failure at a lesser load than the block was originally designed for and usually, an unexpected failure as the signs are minimal.
To resolve this issue, you could consider using a soft attachment block. Our range of Tii blocks is designed for exactly this purpose, to be attached via a rope shackle. Ensuring that you use the correct strength rope for attaching the block should then put your mind at ease as random failure will be less likely to occur, however, It’s important to check these attachments regularly as the rope will still be subject to wear over time but, will show a noticeable wear paten and won’t require a completely new block when its time for a replacement.

Sheaves can sometimes be the failure point in a broken block. These failures occur because the static loads on the block have been too high or the line running around the sheave has acted like a cheese grater. When a block is loaded in a static state it loads up around the sheave unevenly and can cause it to misshape. Once the sheave has misshaped several issues can occur. Firstly, the nylon can crack causing the sheave to break into pieces. Secondly, the misshaped and now oval sheave will allow the ball bearings to drop out or jam the sheave, stopping it from turning.
When a sheave failure happens the first thing to look at is the application and how much dynamic movement the block is required to do. An example of this could be a block used for adjustable shrouds or rig tensioning, a block in these applications will generally not undergo much dynamic movement except when the rig tension is first set or when moving between upwind and downwind settings. The rest of the time it will be subject to lots of static high loads.
A good solution for this problem is to use a block which can withstand static loads better, such as our high load or wire block ranges. These blocks feature a stainless-steel sheave which can withstand the static loads and will not crack or misshape. Another good option for applications that have a high static load and do not require dynamic performance is our range of plain bearing blocks. Plain bearing blocks still utilise a nylon sheave but don’t have any ball bearings. This means more material is used to fill the void where the bearings would usually be resulting in a stronger than usual nylon sheave.
To help you make an even more informed decision below is some more detailed information about each range of blocks. You can also view the complete Allen range here.
Dynamic Blocks

Our Dynamic range of blocks covers sizes from 20mm to 60mm and is available with a variety of accessories such as cleats, swivels, hooks and beckets.
Bearings – The complete Dynamic range features our patented bearing system which uses twin rows of stainless-steel ball bearings running on a stainless-steel rail. This provides a superior load-carrying ability and longevity when compared to other bearing systems which run on a plastic rail.
Ultra-Strap – Our patented Ultra-Strap is used in our 20, 30 & 40mm Dynamic blocks. The Ultra-Strap is unique when compared to other designs because of its coining process. This process strengths the strap, making it more reliable and hard-wearing as well as making it much more rope friendly than other designs. The Ultra-Strap was the first marine industry strap designed to work specifically with a rope attachment.
Becket – The 20 & 30mm Dynamic range offers a large central rivet which not only reduces the overall weight but also offers a rope friendly attachment, perfect as a tie-off point when being used in a cascade system. The 40, 50, and 60mm ranges also feature a large central hole for the same benefits.
Locking Swivel – The 50 & 60mm ranges are designed with a full 360 swivel at the head of the block. This swivel can be locked in two orientations via the small black switch at the top of the cheek. This allows for the option of a fully swivelling block or a permanently locked position.
Tii Blocks
Our range of Tii blocks is the modern design for soft attachment. The range features the same bearing system as our Dynamic range but loses the Ultra-Strap to save weight. What differentiates our Tii blocks from other tie on designs is the large stainless-steel ring at the head of the block. This ring is designed to stop the block from capsizing once tied into a system as well as reducing the chance of the cheeks splitting apart. However, when splicing these blocks to an attachment that is wider than the block, a boom for example, it is still recommended that a cross splice is used to reduce the chance of splitting the cheeks.
High Load Blocks
High Load Blocks fit between the standard dynamic range and the XHL range. The blocks feature a stainless-steel sheave which runs on a double race of stainless-steel ball bearings. By utilising a stainless-steel sheave with a slight V shape profile, the Allen High Load range offers the ability to be paired with both wire and Dyneema®. This design also reduces the deformation of the sheave under high static loads. These combinations result in less friction, higher working loads, better performance and durability over the acetal sheave Dynamic Block range.
XHL Blocks
This range has been designed to deal with extremely high loads without compromising on low load dynamic performance. By combining the Allen patented dynamic bearing technology with a plain bearing peek washer we have created a bearing technology that has extreme dynamic performance even after being subject to static loads of up to 1500Kg. Coupled with CNC machined aluminium side cheeks and a precision turned stainless-steel sheave the range is perfect for use in vang cascades or halyard turning points where loads can be extremely high.
Wire Blocks (High Tension)

Previously known as high tension blocks – this range was originally designed for use in applications where wire was used before Dyneema® was a common replacement. This range uses stainless-steel side cheeks to give maximum strength in the smallest form possible. The sheave runs on a single row of stainless-steel ball bearings with spacers to allow for a much narrower form than our other ranges.
Plain Bearing Blocks

Plain bearing blocks offer great static loading capabilities at a low weight and cost. This makes them perfect for take-up systems or applications that don’t require high dynamic performance. Our range is made using 100% recycled plastics and reuses the outer cheek and ultra-strap from the 20 and 30mm dynamic range to utilise component parts. The range has a grey sheave to differentiate it from the black sheave of the dynamic range.
For more information on any of the above please get in touch with the Allen sales team – Sales@allenbrothers.co.uk – you can also check out the complete manufacturing process of a 60mm Tii block in the following video.